What is MIS Package Substrate?
MIS Package Substrate Manufacturer.MIS Package Substrate (MIS package substrate), as a core component in the field of electronic engineering, plays a key role in connecting and supporting integrated circuit chips and other electronic components. Its design and manufacturing process directly affect the performance and reliability of electronic equipment.
First, the MIS Package Substrate provides electrical connection functions. In modern electronic equipment, various electronic components need to be connected to each other to achieve normal operation. MIS Package Substrate realizes the transmission and conversion of electrical signals through circuit wiring and welding technologies, ensuring effective communication between various components.
Secondly, MIS Package Substrate also undertakes the important task of mechanical support. Electronic equipment usually needs to withstand vibration and shock under various environmental conditions, and MIS Package Substrate, as one of the basic structures, must have sufficient mechanical strength and stability to ensure the stability and reliability of the entire equipment.
In addition, MIS Package Substrate also has good heat dissipation performance. As electronic devices become more and more powerful, they generate more and more heat, so effective heat dissipation measures must be taken to prevent overheating damage. MIS Package Substrate effectively conducts heat to the external environment by designing a reasonable heat dissipation structure and selecting appropriate heat dissipation materials to maintain the stable operation of the equipment.
In short, MIS Package Substrate is not only the infrastructure of electronic equipment, but also a key element to ensure its normal operation and reliability. By providing functions such as electrical connection, mechanical support, and heat dissipation, it provides important support for the design and manufacturing of various electronic devices and promotes the continuous progress and development of electronic technology.
MIS Package Substrate design Reference Guide.
MIS Package Substrate is a key electronic component that connects and supports integrated circuit chips and other electronic components. Its design principles cover many aspects to ensure the performance and reliability of electronic equipment.
First of all, the circuit layout needs to be considered when designing the MIS Package Substrate. Good circuit layout can minimize signal interference and crosstalk and improve circuit stability and reliability. By rationally laying out signal lines, power lines, and ground lines, the transmission loss of the circuit can be reduced and signal integrity improved.
Secondly, mechanical support needs to be considered when designing the MIS Package Substrate. Not only does it need to be able to firmly support integrated circuit chips and other components, it also needs to be able to withstand shock and vibration from the external environment. Therefore, mechanical properties such as structural strength, stiffness, and earthquake resistance need to be considered in the design to ensure that the MIS Package Substrate can maintain stability in various environments.
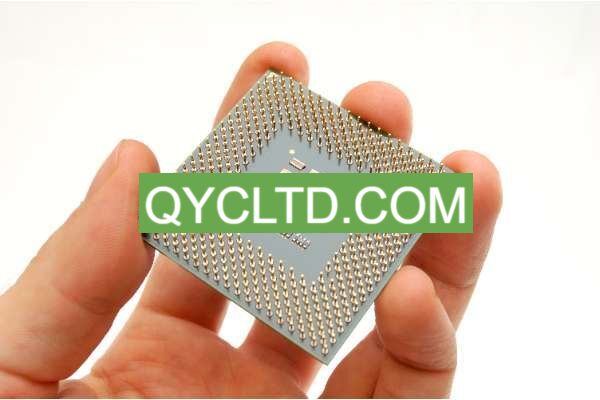
MIS Package Substrate Manufacturer
In addition, heat dissipation is one of the key factors to consider when designing MIS Package Substrate. As the integration and power density of electronic devices increases, heat generation is also increasing, so good heat dissipation design is crucial. Factors such as heat dissipation structure, heat dissipation materials, and heat dissipation paths need to be considered in the design to effectively remove heat and maintain the stable operation of electronic equipment.
In addition, size and layout are also important factors to consider when designing MIS Package Substrate. Reasonable size design can save space to the maximum extent and improve the integration and performance density of electronic equipment. Proper layout design can minimize signal transmission paths and circuit lengths, and improve signal transmission speed and reliability.
In short, designing MIS Package Substrate requires comprehensive consideration of multiple factors such as circuit layout, mechanical support, heat dissipation, and size layout to ensure the best performance and reliability of electronic equipment. Through reasonable design principles, the performance and reliability of MIS Package Substrate can be effectively improved and the continuous innovation and development of electronic equipment can be promoted.
What material is used in MIS Package Substrate?
MIS Package Substrate is one of the most crucial components in modern electronic equipment, and the materials used directly affect its performance and scope of application. Typically, MIS Package Substrate uses a variety of materials, including fiberglass reinforced epoxy resin (FR-4), polyimide (PI), polyamide (PA), etc. Each of these materials has unique characteristics that make them play an important role in different application scenarios.
First, fiberglass reinforced epoxy (FR-4) is one of the most common materials in MIS Package Substrate. It has excellent mechanical strength and good heat resistance, making it suitable for most general electronic applications. FR-4 material has stable electrical properties, low dielectric constant and dielectric loss, which helps improve circuit performance and stability.
Secondly, polyimide (PI) is a high-performance engineering plastic that is often used in electronic applications that require high temperature and high-frequency environments. PI has excellent high temperature resistance and excellent electrical properties, allowing it to maintain stable performance in extreme environments. Therefore, MIS Package Substrate uses substrates made of PI materials that are often used in aerospace, automotive electronics, communication equipment and other fields.
In addition, polyamide (PA) is also a common MIS Package Substrate material. It has good heat resistance and mechanical strength, making it a stable and lower-cost option. PA materials are usually used in some electronic devices that have less stringent performance requirements, such as consumer electronics and industrial control systems.
In general, MIS Package Substrate uses a variety of materials, each of which has its specific advantages and scope of application. Whether it is FR-4, PI or PA, they all provide stable electrical connection, mechanical support and high temperature resistance for electronic equipment, providing a solid foundation for the development of modern electronic technology.
What size are MIS Package Substrate?
The size of the MIS Package Substrate is one of the crucial factors in its design and manufacturing process. Its size depends not only on the required circuit functionality and performance, but also on the application area and other electronic components integrated. Therefore, MIS Package Substrate can be customized according to specific application requirements, ranging from tiny chip-scale packaging to large electronic system-level packaging to meet the needs of electronic devices of different sizes.
First, let’s look at tiny chip-scale packaging. In many modern electronic devices, especially portable devices such as smartphones, tablets, and wearable devices, the requirements for size and weight are very strict. In these cases, the MIS Package Substrate needs to be extremely small in size to allow integration with other tiny components and ensure compactness and portability of the overall device. Through precise design and manufacturing processes, micro-sized MIS Package Substrate can be realized, thus providing important support for the development of modern portable electronic devices.
In contrast, for some large electronic systems, such as data center servers, industrial automation equipment, and communication base stations, the MIS Package Substrate may require larger size and higher integration. These systems often need to accommodate a large number of electronic components and complex circuit structures, so they need to be large enough to accommodate these components and provide them with sufficient space and electrical connections. Therefore, in these application scenarios, MIS Package Substrate often has a larger size to meet the performance and functional requirements of the device.
In addition to the size itself, the thickness and shape of the MIS Package Substrate may also vary depending on specific application needs. For example, some applications may require thinner packages to achieve higher integration and better thermal performance, while other applications may be more concerned with the structural stability and mechanical strength of the package.
To sum up, the size of MIS Package Substrate is customized according to specific application requirements, from tiny chip-scale packaging to large electronic system-level packaging to meet the needs of different sizes and types of electronic devices. Through precise design and manufacturing processes, MIS Package Substrate of various sizes can be realized, providing unlimited possibilities for the development of the modern electronics industry.
The Manufacturing Process of MIS Package Substrate.
Manufacturing MIS Package Substrate (MIS package substrate) is a complex and precise process that involves multiple key steps and requires a high degree of process control and quality management from initial design to final production.
First, the manufacturing process begins with the design phase. At this stage, engineers use tools such as CAD software to design circuit layouts and packaging structures. They need to consider factors such as the functional requirements of the circuit, the mechanical strength and heat dissipation performance of the packaging structure, to ensure the rationality and feasibility of the design.
Next is prototyping. At this stage, the designed circuit layout and packaging structure are used to create prototype samples. Typically, rapid prototyping technology (such as 3D printing) is used to produce samples for functional verification and performance testing. The prototyping process requires a high level of precision and skill to ensure the quality and reliability of the sample.
Then comes the production phase. Once the prototype sample is verified, it will enter the mass production stage. During the production process, PCB manufacturing equipment and process flows are used to apply the designed circuit layout and packaging structure to actual production. This includes converting the circuit diagram into an actual circuit board (PCB) and applying the packaging structure to the circuit board.
Then comes the testing phase. After production is completed, strict functional testing and performance evaluation of MIS Package Substrate are required. This includes circuit connection testing, signal integrity testing, thermal performance testing, etc. Through testing, you can ensure that the product meets the design specifications and has stable performance and reliability.
Finally, there is quality control. Quality control is crucial throughout the entire manufacturing process. Through strict quality management and process control, each manufacturing step can be ensured to meet standards and requirements. This includes the selection of raw materials, maintenance of production equipment, training of operators, etc. Only by maintaining a high level of quality control can stable and reliable MIS Package Substrate products be produced.
In short, the process of manufacturing MIS Package Substrate requires multiple key steps such as design, prototyping, production, testing and quality control. Only through strict process control and quality management can the stability and reliability of products be ensured, thereby meeting the high performance and reliability requirements of modern electronic equipment.
The Application area of MIS Package Substrate.
MIS Package Substrate, as a key electronic component, plays an indispensable role in modern electronic equipment. Its application fields are wide, covering a variety of electronic devices, providing them with stable electrical connections and reliable performance support. The following are the specific applications of MIS Package Substrate in several major application fields:
In smartphones, MIS Package Substrate is used to connect and support various integrated circuit chips, including processors, memories, communication chips, etc. It provides high-speed data transmission, stable power connection, and effective heat dissipation for smartphones, ensuring the performance and stability of the phone.
Similar to smartphones, tablets also require MIS Package Substrate to support their various integrated circuit chips. MIS Package Substrate’s high-density integration and excellent electrical performance enable tablet computers to achieve higher performance and faster data transmission speeds, meeting users’ needs for a smooth experience.
In large data centers, computer servers are responsible for storing and processing massive amounts of data. MIS Package Substrate plays a role in connecting and supporting various processors, memory and network chips in the server, ensuring the stable operation and efficient data processing capabilities of the server.
With the continuous development of automotive electronic technology, modern cars are equipped with more and more electronic devices, such as on-board navigation, intelligent driving assistance systems, etc. MIS Package Substrate plays a key role in automotive electronics, supporting various control units and sensors, providing reliable electrical connections and data exchange, and improving the safety and intelligence of automobiles.
In the field of medical equipment, MIS Package Substrate is widely used in various medical imaging equipment, monitoring instruments and diagnostic equipment. It provides high-speed data transmission and stable power connection for these devices, ensuring the accuracy and reliability of medical equipment, and providing better diagnosis and treatment support for medical staff.
In short, MIS Package Substrate, as a key electronic component, plays an important role in many fields such as smartphones, tablets, computer servers, automotive electronics, and medical equipment. Its stability, reliability and high-performance characteristics provide a solid foundation for the development and application of modern electronic equipment.
What are the advantages of MIS Package Substrate?
As one of the core components of modern electronic equipment, MIS Package Substrate’s advantages cannot be ignored. These benefits will be discussed in depth below to better understand their importance in the electronics industry.
First, MIS Package Substrate has the advantage of high-density integration. As the functions of electronic devices continue to increase and their size shrinks, the requirements for high-density integration of packaging substrates are becoming higher and higher. MIS Package Substrate can integrate more components in a limited space and improve the integration of circuits, making electronic devices more compact and lightweight.
Secondly, MIS Package Substrate has good electrical properties. It can provide stable electrical connections and ensure signal transmission efficiency and reliability between electronic components. By optimizing circuit layout and design, signal loss and interference can be minimized, ensuring optimal performance of electronic devices.
In addition, MIS Package Substrate has excellent heat dissipation performance. As the power of electronic devices continues to increase, heat dissipation issues have become an important factor restricting their performance. MIS Package Substrate can effectively conduct heat away from electronic components and maintain stable operation of the device by properly designing the heat dissipation structure and selecting appropriate heat dissipation materials.
In addition, MIS Package Substrate has the advantage of size flexibility. It can be customized and designed according to specific application requirements, and can be a tiny chip-scale package or a large electronic system-level package to meet the needs of electronic equipment of different sizes and functions.
Finally, MIS Package Substrate has the advantage of being cost-effective. Compared with traditional packaging technology, MIS Package Substrate can achieve higher automation and integration during the manufacturing process, reducing manufacturing costs. At the same time, due to its excellent electrical performance and heat dissipation performance, it can improve the reliability and service life of electronic equipment and reduce maintenance and replacement costs.
To sum up, MIS Package Substrate has become an indispensable part of modern electronic equipment due to its advantages such as high-density integration, good electrical performance, excellent heat dissipation performance, size flexibility and cost-effectiveness. With the continuous development and innovation of electronic technology, I believe that MIS Package Substrate will play a more important role in the future and promote the electronic industry to new heights.
FAQ
How is MIS Package Substrate different from traditional PCB?
There are differences in design, materials and applications between MIS Package Substrate and traditional PCB. Traditional PCB is mainly used for circuit connection and support, while MIS Package Substrate focuses more on the packaging and connection of integrated circuit chips. In addition, MIS Package Substrate uses more advanced materials and manufacturing processes to meet the needs of high performance and high-density integration.
What is the heat dissipation performance of MIS Package Substrate?
MIS Package Substrate has excellent heat dissipation performance, mainly due to its material selection and design optimization. For example, using materials with good thermal conductivity and effective heat dissipation design can effectively conduct the heat generated by the chip to the external environment and maintain a stable operating temperature of the chip.
What environmental conditions is MIS Package Substrate suitable for?
MIS Package Substrate can be applied to various environmental conditions, including normal temperature, high temperature, humidity and high pressure. Its materials and design have been rigorously tested and verified to ensure stable performance and reliability in different working environments.
What factors need to be considered in the design of MIS Package Substrate?
There are many factors to consider when designing MIS Package Substrate, including circuit layout, signal integrity, power consumption distribution, heat dissipation design, size and cost, etc. Proper design can ensure the performance and reliability of electronic equipment while reducing production costs.
How complex is the manufacturing process of MIS Package Substrate?
The process of manufacturing MIS Package Substrate is relatively complex and involves multiple steps, including design verification, prototyping, production processing, testing and quality control. Each step requires precise process control and strict quality management to ensure the stability and reliability of the final product.