What is SOP Package Substrate?
SOP Package Substrate Manufacturer.The SOP 패키지 기판 Manufacturer specializes in crafting intricate substrates for semiconductor packaging. With precision engineering and cutting-edge technology, they produce substrates tailored to meet the stringent demands of modern electronics. From miniature circuitry to complex microstructures, their expertise ensures optimal performance and reliability. Their commitment to innovation drives them to continually refine their processes, staying at the forefront of the industry. As a trusted supplier, they play a vital role in enabling the seamless integration of semiconductor components, empowering devices with enhanced functionality and efficiency.
As a key component in the electronics manufacturing industry, SOP package substrate (System on Package Substrate) plays an important role in connecting and supporting electronic components. It is designed to reliably connect electronic components such as chips, 저항기, and capacitors together to form an overall circuit system. SOP packaging substrates are usually composed of multi-layer insulating substrates, including inner and outer layers of copper foil, and dielectric layers. These layers are stacked together to form the complete packaging substrate through a series of process steps.
In an SOP package substrate, electronic components are arranged on the surface of the substrate and connected to the circuits on the substrate through soldering or other connection techniques. These connection points not only provide a transmission path for electronic signals, but also provide support for power and ground. 또한, SOP packaging substrates can also provide heat dissipation functions to help manage the heat generated by chips and other components to ensure the stable operation of electronic devices.
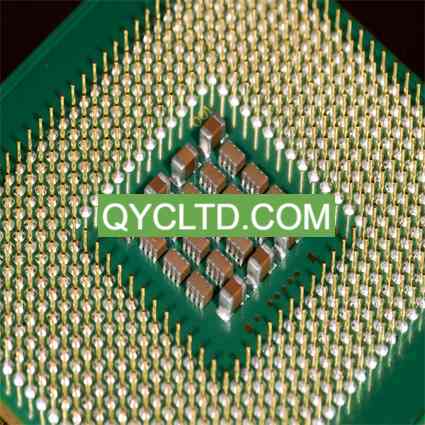
SOP 패키지 기판 제조업체
Due to its compact design and versatility, SOP packaging substrates are widely used in a variety of applications. They are commonly found in mobile devices, smart home products, automotive electronics, communication equipment and other fields. In these applications, SOP packaging substrates not only provide connections between electronic components, but also provide important support for the performance and reliability of electronic products by minimizing space occupation and optimizing heat dissipation design.
전반적, SOP packaging substrates play an indispensable role in modern electronic manufacturing. They not only provide support and connections for electronic components, but also provide important solutions for the design and performance optimization of electronic products.
SOP Package Substrate design Reference Guide.
When designing SOP packaging substrates, engineers need to consider multiple factors to ensure that the final product has excellent performance and reliability. Below is a complete design reference guide covering the main elements to consider when designing SOP package substrates:
Good circuit layout is the key to ensuring stable performance of SOP packaging substrates. During the design process, attention should be paid to the reasonable layout of each functional module and to minimizing the length and intersection of signal lines to reduce the possibility of signal crosstalk and interference. 동시에, ensure that the power and ground wires are properly laid out to provide a stable power supply.
Maintaining signal integrity is critical to SOP package substrate design. Engineers need to pay attention to issues such as impedance matching of signal transmission lines, distance between signal lines, and separation of signal lines and ground lines to minimize signal attenuation and distortion. 또한, appropriate shielding and filtering measures should be taken to suppress the impact of noise and interference on the signal.
The SOP packaging substrate will generate a certain amount of heat during the working process, so good heat dissipation design is crucial. Engineers should reasonably design the heat dissipation structure, including heat sinks, heat dissipation holes, 등., to improve heat dissipation efficiency. 또한, appropriate heat dissipation materials and heat dissipation methods should be selected to ensure stable operation of electronic components in high temperature environments.
요약하면, the design of SOP packaging substrate requires comprehensive consideration of multiple factors such as circuit layout, 신호 무결성, and heat dissipation effect. A complete design reference guide will provide engineers with the necessary guidance and advice to ensure successful implementation and optimal performance of their designs. 다음 지침에 따라, engineers can design SOP packaging substrates with stable performance and high reliability to meet the needs of various application scenarios.
What material is used in SOP Package Substrate?
SOP packaging substrate is a vital component of modern electronic equipment, and the materials used play a vital role in its performance and reliability. 일반적 으로, SOP packaging substrates are made of a variety of materials, including fiberglass, epoxy resin, and polyimide.
Fiberglass is a common substrate material with high strength and stiffness, as well as good corrosion resistance. Its application in SOP packaging substrates can provide good mechanical support and ensure the stable fixation of electronic components, thereby improving overall reliability.
Epoxy is another commonly used material that offers excellent adhesion and chemical resistance. It forms a strong substrate structure during the manufacturing process while providing good electrical insulation properties, helping to protect circuits from interference from the external environment.
또한, polyimide is a high-performance engineering plastic with excellent mechanical properties and high temperature resistance. Its application in SOP packaging substrates can ensure the stable operation of circuit boards in high-temperature environments, while providing excellent corrosion resistance and is suitable for various harsh industrial environments.
The selection of these materials depends not only on their individual performance characteristics, but also on the requirements and budget constraints of the specific application. By rationally selecting and combining these materials, the best performance and reliability of the SOP packaging substrate can be achieved in various application scenarios.
요약하면, the various materials used in SOP packaging substrates provide good mechanical properties, electrical properties and high temperature resistance, allowing them to adapt to various application scenarios and provide important support for the functions and performance of modern electronic products. .
What size are SOP Package Substrate?
The size of the SOP package substrate is one of the crucial considerations in the design process. They not only determine the overall size of the electronic device, but also directly affect the circuit layout and performance. In the modern electronics industry, SOP packaging substrates are available in a wide range of sizes and can be customized to specific application requirements.
For micro-sized SOP packaging substrates, they are mainly used in portable devices, 스마트 폰과 같은, 정제, wearable devices, 등. Due to the volume limitations of these devices, micro-sized SOP packaging substrates need to have an extremely high level of integration and compact layout to ensure the functionality and performance of the entire device. 또한, micro-sized SOP packaging substrates usually adopt advanced manufacturing processes such as SMT (Surface Mount Technology) and COB (Chip on Board) technology to achieve higher performance and reliability.
For large-sized SOP packaging substrates, they are mainly used in large systems such as industrial equipment, communication base stations, and servers. These devices usually need to process large amounts of data and signals and have high performance requirements. 그러므로, large-sized SOP packaging substrates need to have more I/O interfaces and more complex circuit layouts to meet their functional requirements. 또한, large-sized SOP packaging substrates also need to have good heat dissipation performance and mechanical strength to ensure long-term stable operation.
일반 사항, SOP packaging substrates are available in a wide range of sizes and can be customized according to specific application needs. Whether in micro or large sizes, SOP packaging substrates play a key role in supporting the functionality and performance of modern electronic devices. With the continuous development of technology, I believe that SOP packaging substrate will show its importance and application value in more fields.
The Manufacturing Process of SOP Package Substrate.
The manufacturing process of SOP packaging substrate is a complex and precise process involving multiple key steps, each of which has a direct impact on the quality and reliability of the final product. The following are the main steps of the SOP packaging substrate manufacturing process:
The first step in manufacturing SOP packaging substrates is printing. 이 단계에서, the substrate material is usually one or more layers of fiberglass-reinforced epoxy (FR-4) covered with a layer of copper foil. The designed circuit pattern is printed on the surface of the copper foil to form the required circuit connections.
Next comes the electroplating process, where the original copper foil is thickened by plating a layer of copper on the surface of the printed substrate. The purpose of this is to increase the conductivity of the circuit connection, ensure stable transmission of electrical signals, and provide better processing performance for subsequent steps.
Etching is the process of removing unwanted copper foil from the surface of a substrate. By applying a chemical solution or high-pressure water flow to a specific area, the unnecessary copper foil is gradually removed, leaving the designed circuit pattern. This step ensures the precision and accuracy of the circuit.
Drilling is to form connection holes and mounting holes on the SOP package substrate. These holes are used to connect different layers of the circuit board and to mount components. The location and size of the drilled holes must be strictly in accordance with the design specifications to ensure that the components can be installed accurately in the designated locations.
The final step is assembly, where the electronic components are mounted on the SOP package substrate and held in place by soldering or other connection methods. This step requires a high degree of precision and skill to ensure a solid connection between the component and the substrate without causing damage to the circuit.
The precise execution of these steps is the key to ensuring the quality and reliability of SOP packaging substrates. Any inaccuracy or mistake in any step may lead to defects in the final product, thus affecting the performance and stability of electronic products. 그러므로, strict quality control and process management are indispensable when manufacturing SOP packaging substrates.
The Application area of SOP Package Substrate.
As a core component in modern electronic manufacturing, SOP Package Substrate plays an important role in various fields and provides key support for the functions and performance of various electronic products. The following is a detailed introduction to the main application areas of SOP packaging substrates:
소비자 가전 분야에서, SOP packaging substrates are widely used in smartphones, 정제, laptops, digital cameras and other devices. They play a role in connecting and supporting core components such as chips, processors, and memories in these devices, while providing stable electrical connections and signal transmission.
자동차 전자 분야, SOP packaging substrates are used in vehicle electronic control units (ECU), vehicle entertainment systems, driving assistance systems, 등. They are responsible for connecting and supporting various sensors, controllers, communication modules and other equipment in automotive electronic systems to ensure the safety, performance and comfort of the vehicle.
The field of medical equipment has extremely high requirements for reliability and accuracy. SOP packaging substrates play an important role in medical imaging equipment, medical monitoring equipment, implantable medical devices, 등. They provide highly integrated circuit connection solutions for medical equipment, ensuring the stability, accuracy and reliability of the equipment.
In the field of industrial control, SOP packaging substrates are widely used in PLC (프로그래밍 가능한 로직 컨트롤러), 센서, motion control systems, 등. They provide reliable electrical connections and control functions for industrial automation systems, realizing automation, intelligence and precision in factory production processes.
일반 사항, the application scope of SOP packaging substrates covers various fields such as consumer electronics, automotive electronics, 의료 장비, industrial control, 등., providing key support for the functions and performance of modern electronic products. With the continuous development and innovation of science and technology, SOP packaging substrates will continue to play an important role in promoting the progress and development of the electronic industry.
What are the advantages of SOP Package Substrate?
As a core component of modern electronic manufacturing, SOP Package Substrate has many significant advantages over traditional circuit connection methods. These advantages make it the first choice for many electronic devices.
첫, the SOP packaging substrate has a higher level of integration. By integrating multiple electronic components on a unified substrate, the SOP packaging substrate achieves a high degree of circuit integration, making the overall circuit layout more compact, thereby saving space and reducing the volume and weight of the system. This is particularly important for electronic products that need to be designed as compactly as possible, 스마트 폰과 같은, wearable devices, 등.
둘째, the SOP packaging substrate has better heat dissipation performance. Since the SOP packaging substrate is usually made of excellent thermal conductive materials and has a large surface area, it can effectively conduct and dissipate heat, so it can effectively reduce the operating temperature of electronic components and improve the stability and reliability of the system. This is particularly critical for high-performance electronic equipment, such as computers, 서버, 등., which can effectively avoid performance degradation or damage caused by overheating.
또한, the SOP packaging substrate also has lower circuit impedance. Through precise manufacturing processes and high-quality material selection, SOP packaging substrates can achieve lower circuit impedance, thereby improving the speed and stability of signal transmission. This is of great significance for applications that require high-speed data transmission, such as communication equipment, network equipment, 등., and can ensure the stability and reliability of data transmission.
일반 사항, the many advantages of SOP packaging substrates, including higher integration, better heat dissipation performance, lower circuit impedance, 등., make it the first choice for many electronic devices. With the continuous development and popularization of electronic products, the application scope of SOP packaging substrates will further expand and play a more important role.
자주 묻는 질문(FAQ)
What is the life cycle of SOP packaging substrate?
The life cycle of SOP packaging substrates depends on multiple factors, including usage environment, operating conditions and material quality. 일반적으로 말하자면, SOP packaging substrates have a long service life and can last for many years or even more than ten years. 그렇지만, in harsh working environments, 고온과 같은, high humidity or strong vibration, its lifespan may be affected.
What temperature ranges can SOP package substrates be used in?
SOP package substrates typically operate within a temperature range of -40°C to +125°C. This temperature range has covered the working environment of most electronic equipment, including consumer electronics, automotive electronics, industrial control and other fields. 그렇지만, some special applications may require a wider temperature range, so the actual operating conditions need to be taken into consideration when designing and selecting the SOP package substrate.
What is the heat dissipation effect of SOP packaging substrate?
SOP packaging substrates usually have good heat dissipation performance, thanks to their material selection and design optimization. Usually, the surface of the SOP package substrate is designed with heat dissipation holes or heat sinks to increase the heat dissipation surface area and use air flow to accelerate heat dissipation. 또한, the SOP packaging substrate can also be used in combination with a radiator to further improve the heat dissipation effect and ensure that electronic equipment maintains a stable operating temperature during long-term operation.
How to ensure the signal integrity of SOP packaging substrate?
When designing SOP packaging substrates, engineers usually take a variety of measures to ensure signal integrity. This includes using appropriate cabling techniques, avoiding signal interference, reducing signal transmission delays, 등. 또한, the use of high-quality materials and precision manufacturing processes are also key to ensuring signal integrity. Through the comprehensive application of these measures, the SOP packaging substrate can ensure the stability and reliability of the circuit and the accuracy and stability of signal transmission.