What is ABF(Ajinomoto) Substrate?
ABF(Ajinomoto) Substrate Manufacturer.ABF, a renowned name in the industry, stands tall as Ajinomoto Substrate Manufacturer. With a legacy of excellence, they pioneer the production of substrates vital for various applications. Their state-of-the-art facilities ensure premium quality, meeting stringent standards. Through innovative processes and unwavering commitment, ABF consistently delivers top-notch substrates, catering to diverse needs worldwide. As a trusted partner, they empower industries ranging from biotechnology to food production, facilitating advancements and enhancing product quality. ABF’s dedication to excellence cements its position as the premier choice for substrate solutions.
ABF (Ajinomoto) substrate represents an important innovation in PCB manifatturiero. ABF, which stands for American Ginseng Collagen Substrate, is an advanced organic substrate material developed by the Japanese company Ajinomoto. Its research and development stems from the continuous pursuit of electronic product performance and reliability, as well as the continuous exploration and innovation of substrate materials.
This substrate material uses American ginseng collagen as its main ingredient. American ginseng collagen is a natural organic substance with excellent mechanical properties and heat resistance. Through innovation and precise control of process technology, Ajinomoto has transformed American ginseng collagen into an ideal substrate material for PCB manufacturing. This conversion process not only retains the excellent properties of American ginseng collagen, but also gives the ABF substrate more electrical and thermal properties, making it outstanding in electronic devices.
ABF substrate performs well in terms of electrical performance, with low loss, low noise and stable signal transmission characteristics. This makes it ideal for high frequency and high speed circuits. Inoltre, the ABF substrate also has excellent thermal properties, which can effectively disperse and remove the heat generated on the circuit board to ensure the stable operation of electronic components. Its excellent mechanical properties ensure the reliability and durability of electronic equipment in harsh environments such as vibration and shock.
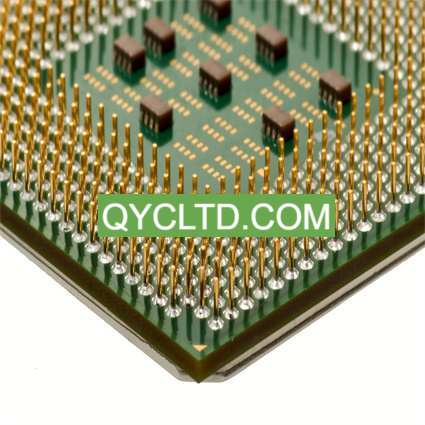
ABF(Ajinomoto) Substrato Fornitore
Pertanto, ABF (Ajinomoto) substrate has become one of the preferred substrate materials in modern electronic devices. It is not only widely used in consumer electronics products, come gli smartphone, Compresse, and so on., but also widely used in automotive electronics, communication equipment, industrial control systems and other fields. Its stable and reliable performance provides strong support for the design and manufacturing of various electronic products, and promotes the continuous development and progress of the entire electronics industry.
ABF(Ajinomoto) Substrate design Reference Guide.
In the design process of modern electronic devices, selecting the appropriate substrate material is crucial. As an advanced organic substrate material, ABF (Ajinomoto) substrate has excellent performance and reliability. Tuttavia, when designing PCB, a series of design guidelines and best practices still need to be followed to ensure that the performance of the final product reaches the expected level. .
The laminated structure of the ABF substrate directly affects its electrical and thermal properties. During the design stage, factors such as signal transmission requirements, Distribuzione dell'energia, ground plane layout, and thermal management should be taken into consideration to rationally design the laminate structure. Generalmente, multi-layer structures provide better signal integrity and thermal distribution, but care needs to be taken to avoid inter-layer coupling and signal interference.
In the wiring design of ABF substrate, certain specifications and guidelines should be followed. This includes signal and power line layout, length matching, impedance control, and pairing of differential signals. Through reasonable wiring specifications, crosstalk and delay in signal transmission can be reduced, and the stability and reliability of the circuit can be improved.
When designing a PCB, pin layout is a crucial aspect. Reasonable pin layout can reduce signal transmission loss and interference, while facilitating assembly and welding. Based on the characteristics of the ABF substrate, the length and bending of the pins should be reduced as much as possible to ensure stable signal transmission and reliable connection.
Since ABF substrates have high thermal stability, good thermal management solutions need to be considered during the design process. This includes reasonable heat dissipation design, optimization of heat conduction paths, and placement of thermal sensors. Through effective thermal management, the operating temperature of electronic components can be reduced, their service life can be extended, and the stability and reliability of the system can be ensured.
Riassumendo, the design reference guide for ABF substrate covers laminate structure, wiring specifications, pin layout and thermal management. Following these guidelines and best practices can help engineers take full advantage of ABF substrates and maximize PCB performance and reliability. Durante il processo di progettazione, it is recommended to work closely with the ABF substrate supplier to obtain professional technical support and advice to ensure the smooth implementation of the design and the successful launch of the final product.
What material is used in ABF(Ajinomoto) Substrate?
ABF (Ajinomoto) substrate is an advanced organic substrate material, and its material composition plays a vital role in PCB manufacturing. The materials of ABF substrates are carefully selected and optimized to ensure that they have excellent electrical, thermal and mechanical properties to meet the needs of different application scenarios.
The core material of the ABF substrate is American ginseng collagen, a high-performance organic material with excellent insulation properties and heat resistance. American ginseng collagen has good chemical stability, is not susceptible to moisture or water absorption, and can maintain stable performance under various environmental conditions. Its unique molecular structure gives the ABF substrate good electrical properties, such as low dielectric constant and low loss tangent, which is beneficial to improving the speed and stability of signal transmission.
In order to enhance the mechanical strength and heat resistance of ABF substrates, glass fiber reinforcements are usually added to the American ginseng collagen matrix. Glass fiber has excellent strength and rigidity and can effectively improve the flexural strength and impact resistance of the substrate. By adjusting the content and distribution of glass fibers, customized designs of ABF substrates can be achieved to meet the needs of different application scenarios.
In order to improve the surface flatness and solderability of the ABF substrate, a layer of special treatment material is usually coated on the surface. This treatment material not only provides good welding performance, but also protects the substrate surface from the external environment. Common treatment materials include organic and metallic compounds that can effectively improve the reliability and stability of welding contacts.
In order to improve the flame retardant performance and processing performance of ABF substrates, a certain amount of flame retardants and plasticizers are usually added to the material. These additives can effectively inhibit the burning of substrates in high-temperature environments while improving the flexibility and processability of the material. Through reasonable formula design and processing technology, the excellent performance and stability of ABF substrates can be achieved.
Riassumendo, the material composition of ABF (Ajinomoto) substrate is carefully designed and optimized to achieve the best electrical, thermal and mechanical properties. This advanced substrate material provides important support for the design and manufacturing of modern electronic equipment, bringing users a more stable and reliable product experience.
What size are ABF(Ajinomoto) Substrate?
The material and size of the ABF substrate are crucial considerations during the design and manufacturing process. These aspects directly affect the performance, reliability and scope of application of the substrate.
The ABF substrate uses American ginseng collagen as the main material, which is an organic substance with excellent mechanical properties and stability. Compared with traditional substrate materials, such as FR-4, American ginseng collagen provides higher heat resistance and chemical resistance. Inoltre, the ABF substrate is combined with glass fiber reinforcements to further enhance its mechanical strength and stability. This combination of materials allows ABF substrates to maintain stable performance under extreme conditions, such as high temperature environments or high humidity environments.
The flexibility of ABF substrates is also reflected in its size customization. Since different applications have different substrate size requirements, ABF substrates can be customized to meet the needs of specific applications. From small mobile devices, such as smartphones and tablets, to large server systems, ABF substrates can be flexibly adapted. This customizability makes ABF substrates ideal for a variety of application scenarios.
Inoltre, size customization of ABF substrates can also optimize circuit layout and heat dissipation design, thereby improving overall system performance and reliability. Engineers can adjust the size and layout of the ABF substrate based on the device’s space constraints and heat dissipation needs to achieve the best working results.
Riassumendo, the material and size design of the ABF substrate fully consider the working requirements and space constraints of electronic products in different environments. By using high-quality materials such as American ginseng collagen and flexibly customizing sizes, ABF substrates provide a reliable foundation for the performance and reliability of electronic products.
The Manufacturing Process of ABF(Ajinomoto) Substrate.
During the PCB manufacturing process, the production of ABF substrates undergoes a series of precise steps to ensure the high quality and reliability of the final product.
Primo, the manufacturing process begins with the preparation of the substrate material. The main component of the ABF substrate is American ginseng collagen, a high-performance organic material. Before production, raw materials need to be strictly screened and processed to ensure quality consistency and stability.
Next is the graphic design stage. In questa fase, engineers use CAD software to design and determine the PCB’s routing, lamination structure, and component layout. This process is critical because the quality of the design directly affects the performance and reliability of the final product.
Una volta completato il design, it’s time to laminate and process. In questa fase, each layer of the ABF substrate is laminated with other layers under strictly controlled temperature and pressure. This ensures a strong bond between the layers while maintaining the flatness and stability of the PCB board. Subsequently, the plate is cut and drilled using CNC machining equipment to make it meet the design requirements.
Throughout the entire manufacturing process, strict quality control is indispensable. By using advanced process technology and equipment, such as automated inspection systems and precision processing equipment, it is possible to ensure that every link meets standards and ultimately produce ABF substrate products with consistent quality and reliability.
Grembiule, the manufacturing process of ABF substrates is a precise and complex process involving multiple key steps. Through strict quality control and precise process technology, we ensure that the quality and performance of the final product meet industry standards, providing a reliable foundation for the performance and reliability of electronic products.
The Application area of ABF(Ajinomoto) Substrate.
As an advanced organic substrate material, ABF substrate has been widely used in various application fields due to its excellent performance and reliability. From consumer electronics to automotive electronics, communication equipment and industrial control systems, ABF substrates play a vital role.
Nel campo dell'elettronica di consumo, ABF substrates are widely used in smartphones, Compresse, smart watches and other devices. These devices have extremely high requirements for stable electrical connections and excellent thermal management. The use of ABF substrates effectively meets these requirements and brings a better experience to users.
In the field of automotive electronics, ABF substrates are used in key components such as automotive electronic control units (ECUs), instrument panels, and navigation systems. As the level of automotive electronics continues to improve, the requirements for the reliability and stability of electronic components are getting higher and higher. ABF substrate plays an important role in the field of automotive electronics with its excellent performance.
In the field of communication equipment, ABF substrates are widely used in base stations, routers, switches and other equipment. These devices require stable signal transmission and efficient thermal management. The use of ABF substrates helps improve the performance and reliability of the devices and ensures the stable operation of the communication network.
In the field of industrial control systems, ABF substrates are used in PLC (programmable logic controller), industrial robots, sensors and other equipment. The industrial environment has extremely high requirements for the stability and reliability of electronic equipment. The use of ABF substrates helps improve the anti-interference ability and long-term stable operation performance of the equipment.
Generalmente, ABF substrates play an important role in various application fields, providing stable electrical connections and excellent thermal management for electronic products, bringing better experience and reliability to users. With the continuous advancement of technology and the continuous expansion of application fields, it is believed that ABF substrates will continue to play an important role in the future electronic field.
What are the advantages of ABF(Ajinomoto) Substrate?
ABF (Ajinomoto) substrate has many advantages over traditional FR-4 substrate, which make it the preferred substrate material for many electronic devices. The following is an expansion of the advantages of ABF substrates:
Primo, ABF substrate has higher heat resistance and mechanical strength. In ambienti ad alta temperatura, ABF substrates can maintain stable performance and are not prone to deformation or failure, making them suitable for more harsh working environments. In contrast, FR-4 substrates may experience material deformation or structural damage at high temperatures, affecting the stability and reliability of electronic devices.
Secondariamente, ABF substrate has more stable electrical performance. Due to the special structure and manufacturing process of the ABF substrate material, it has a lower dielectric constant and loss factor, which can effectively reduce loss and noise in signal transmission. This means that circuits designed on ABF substrates can work more stably and reliably, improving overall system performance and efficiency. In contrast, FR-4 substrates can be affected by material inhomogeneities and manufacturing processes, causing fluctuations and instability in electrical performance.
Inoltre, ABF substrates also have excellent corrosion resistance and reliability. Its material characteristics make the ABF substrate less susceptible to corrosion by chemical substances and able to operate stably for a long time under harsh environmental conditions. This makes the ABF substrate very suitable for some application scenarios that require high reliability, such as aerospace, automotive electronics and other fields. In contrast, FR-4 substrates may suffer performance degradation or failure due to chemical attack, requiring more frequent maintenance and replacement.
Riassumendo, the advantages of ABF (Ajinomoto) substrates lie in its higher heat resistance and mechanical strength, stable electrical performance, and excellent corrosion resistance and reliability. These advantages make ABF substrate the preferred material in the field of electronic equipment manufacturing, providing users with more stable and reliable products and services.
Domande frequenti
What environmental conditions are ABF substrates suitable for?
ABF substrate is a material that is resistant to high temperatures, humidity and vibration, making it suitable for a variety of harsh environmental conditions. They are often used in automotive electronics, industrial control systems, communication equipment, aerospaziale e altri settori, which have extremely high requirements on the reliability and stability of electronic equipment.
What is the difference between ABF substrate and FR-4 substrate?
ABF substrates have a series of advantages over traditional FR-4 substrates. Primo, the ABF substrate has higher heat resistance and can work at higher temperatures without failure. Secondariamente, the ABF substrate has better mechanical strength and better resistance to vibration and impact. Inoltre, the signal transmission performance of the ABF substrate is more stable and can reduce signal loss and noise. Grembiule, ABF substrates can provide higher performance and reliability and are suitable for a wider range of application scenarios.
How long is the production cycle of ABF substrate?
The production cycle of ABF substrates depends on the quantity and complexity of the order. Generale, the production cycle of ABF substrates is relatively short, usually between days and weeks. Tuttavia, for large batch orders or special requirements, the production lead time may be extended. In order to understand the production cycle more accurately, it is recommended to communicate with suppliers and arrange orders in advance.
What is the cost of ABF substrate?
The cost of ABF substrates varies depending on a variety of factors, including material cost, Processo di produzione, order quantity, and special requirements. Compared with traditional FR-4 substrates, the cost of ABF substrates may be slightly higher, but its excellent performance and reliability can often offset this cost increase. When choosing an ABF substrate, you need to comprehensively consider factors such as cost, performance, and reliability, and conduct full communication and negotiation with suppliers.
Does ABF substrate have environmental advantages?
The ABF substrate uses natural materials such as American ginseng collagen, which has certain environmental advantages over some traditional substrate materials. They generate relatively little waste during the manufacturing process and can be recycled with appropriate disposal, reducing their impact on the environment. Tuttavia, it is still very important to ensure that the production and processing processes of ABF substrates comply with environmental standards. Suppliers and manufacturers should follow relevant environmental regulations and guidelines and take effective environmental measures.