What is 3D IC Package Substrate?
3D IC Package Substrate Manufacturer.A 3D IC package substrate manufacturer specializes in producing advanced substrates for three-dimensional integrated circuit packaging. These substrates facilitate the stacking of multiple IC layers, enhancing performance, reducing power consumption, and saving space. By utilizing cutting-edge materials and precision engineering, the manufacturer ensures high reliability and efficiency in electronic devices, catering to industries such as computing, Telekommunikation, and consumer electronics, ultimately driving innovation in the semiconductor industry.
3D IC (three-dimensional integrated circuit) packaging substrate is a technology used to build high-performance and high-density integrated circuit packages. Traditional packaging technology usually packages a single chip on a flat substrate, while 3D IC packaging technology allows multiple chips to be stacked vertically to form a three-dimensional structure. This structure can significantly reduce the packaging footprint and improve system performance and density. 3D IC packaging substrates are usually composed of multiple layers of insulating media and conductive layers, where the conductive layers are used to connect circuits between different chips. Through this structure, chips with different functions can be more closely integrated together, reducing the distance and delay of signal transmission, thereby improving the response speed and energy efficiency of the system. Außerdem, 3D IC packaging can also integrate chips with different process technologies in the same package, thereby improving the flexibility and diversity of the system. Deshalb, 3D IC packaging substrates have broad application prospects in high-performance computing, artificial intelligence, cloud computing and other fields.
3D IC Package Substrate Design Reference Guide.
The 3D integrated circuit packaging substrate design reference guide is to help engineers provide guidance and reference when designing 3D integrated circuit packaging substrates. This guide contains detailed information on design principles, technical specifications and best practices to help engineers overcome the challenges they may encounter during the design process and ensure that the final packaging substrate has high performance, high reliability and excellent electrical performance. characteristic. Topics typically covered by this guide include, but are not limited to: packaging substrate material selection, hierarchical structure design, wiring rules, power management, thermal design, electromagnetic compatibility, Signalintegrität, etc. By following the guidance provided by this guide, engineers can more effectively design compliant 3D integrated circuit packaging substrates to meet growing market demands and technical challenges.
What material is used in 3D IC Package Substrate?
3D IC packaging substrates typically use materials with high thermal conductivity and excellent electrical properties. Among them, a common material is silicon-based substrate. Silicon has good thermal conductivity and mechanical stability, making it suitable for manufacturing 3D IC packaging substrates. Außerdem, silicon-based substrates also have excellent dimensional stability and processability, and can meet micron-level manufacturing requirements.
In addition to silicon-based substrates, other materials can also be used for 3D IC packaging substrates, such as glass substrates, ceramic substrates, etc. These materials typically have high strength, low thermal expansion coefficients, and good electrical properties to meet a variety of requirements in packaging.
In 3D IC packaging, substrate selection is critical to device performance and packaging process. Deshalb, when selecting materials, factors such as thermal properties, mechanical properties, electrical properties, and manufacturing costs need to be comprehensively considered to ensure the stability and reliability of the package.
What size are 3D IC Package Substrate?
The dimensions of 3D IC packaging substrates vary by manufacturer and specific application, often depending on the technology and manufacturing process used. These dimensions can vary in several ways, including length, Breite, and thickness. Generell, the size of these package substrates will be relatively small because they need to be stacked with other packages to form a three-dimensional stacked structure. This structure helps improve integration and performance, but also requires a high degree of precision and process control.
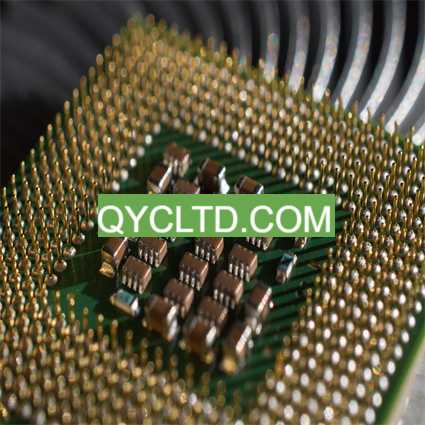
3Hersteller von D-IC-Gehäusesubstraten
The dimensions of most 3D IC packaging substrates range from a few millimeters to tens of millimeters. Aber, these dimensions may change as technology advances and application demands arise. Zum Beispiel, 3D IC packaging substrates used in mobile devices may be smaller than those used in servers or computers. Zusätzlich, some packaging substrates may have very fine dimensions to achieve higher density and performance.
In summary, the dimensions of 3D IC packaging substrates are variable, depend on many factors, and may vary in different applications. The size of these packaging substrates is often limited by the manufacturing technology and manufacturer, and continues to evolve as technology advances.
The Manufacturing Process of 3D IC Package Substrate.
The manufacturing process of 3D IC (three-dimensional integrated circuit) packaging substrates includes multiple key steps that require strict control from design to final assembly. Here are the main steps of this process:
Design and planning: Erste, the 3D IC packaging substrate is designed according to the required functions and specifications. This includes determining circuit layout, connector location and hierarchy, etc. The design process needs to consider aspects such as electrical performance, Thermomanagement, and mechanical strength.
Substrate preparation: According to the design, select the appropriate substrate material, such as silicon (Silicon), glass fiber reinforced resin (FR-4), etc. The substrate is then processed into the desired shape and size through methods such as chemical etching, machining or laser cutting.
Stacked preparation: 3D IC packaging substrates are usually composed of multiple stacked components. In diesem Schritt, various components are arranged and fixed on the substrate according to the design through processes such as film stacking, metallization, and filling materials.
Circuit connection: Connecting circuits at different levels is one of the key steps in 3D IC packaging. Methods such as micro-welding, gold wire bonding or conductive glue are used to connect circuits at all levels to ensure the transmission of signals and power.
Encapsulation and encapsulation: After the circuit connection is completed, the entire structure needs to be encapsulated to protect the circuit from environmental effects and mechanical damage. Commonly used packaging materials include epoxy resin, polyimide (PI), etc. The packaging materials are covered on the circuit surface through processes such as lamination or injection molding and cured.
Testing and quality control: After completing the packaging, the 3D IC package needs to be rigorously tested to ensure that it meets the design specifications and has good electrical performance and reliability. Including electrical testing, thermal analysis and mechanical strength testing, as well as quality control monitoring.
Assembly and packaging: The final step is to assemble the 3D IC packaging substrate with other components (such as heat sinks, pins, etc.) and encapsulate it in a casing to form the final packaged product. The assembly process requires precise positioning and alignment to ensure the quality of the connections between individual components and the integrity of the package.
Through the above steps, the manufacturing process of 3D IC packaging substrate can be completed and high-performance, highly integrated integrated circuit packaging products can be realized.
The Application area of 3D IC Package Substrate.
3D IC packaging substrates have a wide range of applications and play an important role in the electronics industry. This advanced packaging technology has been widely used in many fields, including but not limited to:
Mobile devices: 3D IC packaging substrates play an important role in the field of mobile devices. Zum Beispiel, the compact design of products such as smartphones, Tabletten, and portable audio/video devices poses challenges for innovation in packaging technology. By using 3D IC packaging substrates, higher integration and smaller size can be achieved, providing higher performance and longer battery life for mobile devices.
Computer: In the computer field, especially in high-performance computing and cloud computing, 3D IC packaging substrates are widely used. This packaging technology enables the stacking of multiple processors, memories and other functional units, thereby improving data transmission speed and overall system performance. Außerdem, for scenarios with high performance requirements such as data centers, 3D IC packaging substrates can also provide higher energy efficiency ratios.
Communication equipment: In the field of communication equipment, such as base stations, satellite communication equipment and network routers, there are increasing requirements for high density, high speed and low power consumption. 3D IC packaging substrates enable compact stacking of multiple communication modules, thereby improving device performance and reliability while reducing energy consumption and space requirements.
Automotive electronics: As automotive electronic systems continue to evolve, the demand for high performance, high reliability and compact design is also increasing. 3D IC packaging substrates can help achieve compact stacking of automotive electronic modules, thereby improving system integration and performance, and meeting the requirements of automotive electronic systems for environmental conditions such as temperature, vibration, and humidity.
Industrial automation: In the field of industrial automation, the requirements for high performance, high reliability and long-term stable operation are very high. 3D IC packaging substrates can help achieve compact stacking of functional units such as industrial controllers, sensors and actuators, thereby improving system integration and performance while reducing equipment size and energy consumption.
Kurz gesagt, 3D IC packaging substrates have broad application prospects in various electronic devices and systems, which can help achieve the design goals of higher performance, smaller size and lower energy consumption, and promote the continued development and innovation of electronic technology.
What are the advantages of 3D IC Package Substrate?
3D IC packaging substrates have many advantages, which make them one of the important technologies in today’s integrated circuit field. Here are some of the advantages:
High-density integration: 3D IC packaging substrates can stack multiple chips in the vertical direction to achieve a high degree of integration. This high degree of integration can combine multiple functional modules into one package, reduce package volume, increase device density, and save PCB board area.
Short connection length: In 3D IC packaging, the connection length between chips is significantly shortened. This means faster signal transmission and lower power consumption, while reducing signal transmission delays and improving system performance.
Low power consumption design: Because 3D IC packaging can integrate functional modules more closely together, the circuit path is shorter, so power consumption is lower. Außerdem, power consumption can also be reduced due to more efficient communication between chips.
Superior heat dissipation performance: 3D IC packaging can improve heat dissipation performance by adding heat dissipation layers or heat dissipation modules between multiple chips. This can dissipate heat away from the chip more effectively and keep the system running stably.
Multi-function integration: Since 3D IC packaging can stack multiple chips in the vertical direction, chips with different functions can be integrated together to achieve multi-function integration. This can reduce the number of components required in the system, reduce system complexity, and improve system performance and reliability.
Im allgemeinen, 3D IC packaging substrates have brought new development opportunities to the field of integrated circuits and promoted electronic products by improving integration, reducing connection length, reducing power consumption, improving heat dissipation performance, and achieving multi-functional integration. Continuous innovation and progress.
FQA (Häufig gestellte Fragen)
What is a 3D IC Package Substrate?
A 3D IC Package Substrate is a specialized substrate used in three-dimensional integrated circuit (3D IC) Verpackung. It serves as a foundation for mounting and connecting multiple layers of integrated circuits vertically.
How does a 3D IC Package Substrate differ from traditional substrates?
Unlike traditional substrates, which typically support only a single layer of integrated circuits, a 3D IC Package Substrate facilitates the stacking of multiple layers of ICs. This enables higher levels of integration and functionality in a smaller footprint.
What are the advantages of using a 3D IC Package Substrate?
The primary advantages include increased packaging density, improved performance due to shorter interconnection lengths, reduced power consumption, and enhanced thermal management capabilities. Zusätzlich, 3D IC packaging allows for heterogeneous integration of different technologies, such as logic, memory, and sensors, in a single package.
What are the key considerations when designing with a 3D IC Package Substrate?
Designers must consider factors such as thermal dissipation, Signalintegrität, power delivery, and mechanical reliability. Zusätzlich, they need to ensure compatibility with manufacturing processes for stacking and interconnecting multiple layers of ICs.